Установки неразрушающего контроля валков прокатных станов
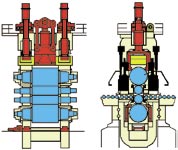
Рис. 1. Схематическое изображение прокатного стана
Рассмотрим сначала процесс прокатного производства. Прокатываемый материал проходит между рабочими валками, которые опираются на опорные валки, тем самым увеличивается жесткость всего прокатного стана. Это позволяет прокатывать металл меньшей толщины. Число опорных валков может достигать 18 штук, по 9 на каждый рабочий валок (при прокате фольги цветных металлов толщиной несколько микрон). При прокате черных металлов используют прокатные станы более простой конструкции с двумя рабочими и двумя опорными валками под названием «квадро» (рис. 1).
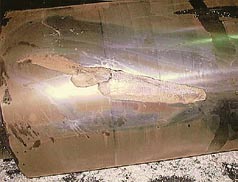
Рис. 2. Сколы на поверхности рабочего валка
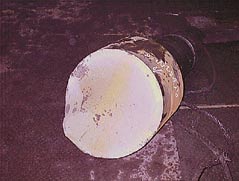
Рис. 3. Разрушение рабочего валка
Рабочие валки изнашиваются, на их поверхности появляются микродефекты. Развиваясь, они могут приводить к сколам (рис. 2) или к полному разрушению валка (рис. 3). Рабочие валки, являясь инструментом, от которого зависит производительность прокатного стана, оказывают большое влияние на качество поверхности и профиль проката.
Проблема быстрого износа рабочих валков породила необходимость увеличения прочности их поверхностного слоя в связи с тем, что они испытывают термический удар и большие знакопеременные нагрузки в процессе проката. Первоначально для этой цели производилось поверхностное упрочнение с применением различных технологий. Однако с увеличением скорости прокатки, ужесточением норм по качеству поверхности проката такие валки перестали удовлетворять все возрастающим требованиям.
Для изготовления высококачественных рабочих валков стали применять двухслойное литье. Внутреннее ядро бочки отливается из чугуна (серого или шаровидного), а рабочий слой – из легированных или высоколегированных (хромистых) сталей. В последние годы в качестве металла для внешнего слоя начали применять полуи даже быстрорежущие стали.
Аварийный выход валков из строя приводит к очень большим затратам (простой стана на многие часы, бракованный прокат, повреждение оборудования). Стоимость высокохромистых валков составляет 30 – 40, а быстрорежущих – 40 – 70 тыс. долларов.
Требования к опорным валкам не такие жесткие, поскольку они работают в менее тяжелых условиях. Для их изготовления в основном используются низкои среднелегированные стали.
Проблеме контроля валков прокатных станов в нашей стране не уделяется должного внимания. В 1980-е гг. был разработан ОСТ 24.023.22-83 [1] для УЗК стальных кованых валков станов горячей прокатки. В этом документе регламентируется процесс ручного УЗК с целью обнаружения только внутренних дефектов опорных валков. Поверхностные дефекты, образующиеся в процессе эксплуатации валков, не контролируются.
До настоящего времени НК рабочих валков в России вообще не предусматривался, если не принимать во внимание визуальный осмотр. В основном это обусловлено отсутствием нормативнотехнической документации. Отметим, что как показано в [2], где приведены результаты исследований по выявлению дефектов в рабочих валках стана горячей прокатки, применение НК позволило уменьшить количество аварий рабочих валков на заводе более чем на 30 %.
За рубежом контролю валков прокатных станов уделяется больше внимания. НК подвергаются как опорные, так и рабочие валки. Контроль осуществляется как на заводах изготовителях, так и периодически в процессе эксплуатации. Для ручного контроля используется МПД, КД, ВД и УЗК. Однако в основном за рубежом контроль рабочих и опорных валков производят с использованием автоматизированных установок, среди которых наиболее известны установки фирм Lismar Engineering B.V. (Голландия), Sarclad (Великобритания), Kantoc (Япония), Innerspec Technologies (США). Проанализируем основные технические характеристики этих установок. Информационной базой явились рекламные материалы фирм-изготовителей и их Интернет сайты.
Известно [3], что причиной разрушения почти 95 % рабочих валков являются поверхностные дефекты. Наши исследования [2] также подтверждают этот факт, хотя по нашим данным эта цифра составляет 80 – 90 %. Поэтому во всех зарубежных автоматизированных установках обязательно проводится контроль с целью обнаружения поверхностных дефектов.
.jpg)
Рис. 4а – общий вид. Установка фирмы Lismar Engineering B.V. (Голландия)
Одними из наиболее известных являются установки Lismar (рис. 4), поставляемые в базовой комплектации только с вихретоковым каналом, что позволяет обнаруживать поверхностные (длиной более 10 мм и глубиной более 0,1 мм) и подповерхностные дефекты на глубинах до 3 мм. Скорость контроля может достигать 2 м/с. Результаты вихретокового контроля выводятся на дисплей в виде двух окон. В верхнем окне – сигналы от трещин, а в нижнем – сигналы, характеризующие структурные изменения валка (прижоги, ушибы и т. д.) (рис. 4б). Используется цветовая градация сигналов. Сигналы зеленого цвета являются допустимыми. Если же наблюдаются сигналы красного цвета, то шлифовщик должен продолжить обработку валка до их исчезновения.
.jpg)
Рис. 4б – дисплей вихретокового канала. Установка фирмы Lismar Engineering B.V. (Голландия)
Для обнаружения внутренних дефектов установки дополнительно оснащаются ультразвуковыми каналами (до четырех штук). В случае глубокозалегающих дефектов применяются прямые ПЭП с частотами менее 1 МГц; глубина контроля составляет от 100 до 1700 мм. Для обнаружения дефектов в рабочем слое валков, а также для контроля границы в двухслойных валках применяют раздельно-совмещенные ПЭП на частоту 4 МГц; глубина контроля при этом составляет от 5 до 125 мм. Для обнаружения дефектов (трещин), ориентированных под углом, применяются два наклонных ПЭП с углами ввода 60° и частотой 4 МГц. Акустические оси этих ПЭП направлены в противоположные стороны вдоль образующей валка, что обеспечивает прозвучивание валка за один проход.
Согласно рекламным проспектам фирмы чувствительность ультразвуковых каналов составляет 20 мм2 (диаметр 5 мм). Из имеющихся материалов не ясно, используется ли в установках система ВРЧ. Отсутствие ВРЧ должно приводить к большим ошибкам при определении эквивалентных размеров дефектов.
.jpg)
Рис. 4в - С-развертка. Установка фирмы Lismar Engineering B.V. (Голландия)
Результаты контроля представляются в виде С-развертки (рис. 4в). Существует возможность наложения результатов вихретокового и ультразвукового контроля на одной развертке.
.jpg)
Рис. 5. Внешний вид установки фирмы SARCLAD (Великобритания)
Фирма Sarclad разработала автоматизированную установку Rollscan (рис. 5), в которой применяется комбинация вихретокового и ультразвукового (с одним раздельно-совмещенным ПЭП) контроля. Рабочая частота ПЭП составляет 2,25 МГц, диапазон глубины контроля 4 – 100 мм.
Линейка из 8 вихретоковых преобразователей позволяет обнаруживать поверхностные трещины длиной 2,5 мм и глубиной от 0,05 до 0,1 мм, а также ушибы длиной 3,0 мм и глубиной 3 мм, имеющие падение твердости более 20 HV. Система позиционирования работает с угловой дискретностью 45° и линейной по оси валка – 12 – 50 мм. Скорость контроля в режиме обнаружения поверхностных дефектов составляет 3 м/с, а в режиме обнаружения внутренних дефектов – около 1 м/с. Результаты контроля представляются в виде двухмерной развертки. Основное назначение этих установок – обнаружение трещин на поверхности валка, дефектов в рабочем слое и расслоений на границе.
.jpg)
Рис. 6. Внешний вид установки фирмы Innerspec Technologies (США)
Фирмой Innerspec Technologies для НК стальных и алюминиевых прокатных валков выпускаются две установки: Тemate® 5500 и Rollmate 5500 (рис. 6). Первая предназначена для УЗК только рабочих валков, а вторая – для контроля рабочих и опорных валков. Эти установки, в которых применяются два ЭМА-преобразователя, предназначены для обнаружения только поверхностных и подповерхностных дефектов и имеют два режима работы. В первом режиме с более высокой чувствительностью глубина контроля составляет 1,5 мм, а втором с пониженной чувствительностью – 6,4 мм. В рекламных проспектах прямо не указывается, какой тип волн используется. По всей видимости, контроль ведется с использованием поверхностных волн. Применение ЭМАП позволило устранить ложные сигналы от капель контактной жидкости. Предусмотрена возможность включения дополнительных преобразователей, которые можно использовать для контроля границы в двухслойных валках. Результаты контроля представляются в виде двухмерной развертки. Эти установки предназначены, в основном, для обнаружения поверхностных дефектов.
-vneshnij-vid-ustanovki-firmy-kantoc-(yaponiya).jpg)
Рис. 7(а). Внешний вид установки фирмы Kantoc (Япония)
-akusticheskij-blok-ustanovki-firmy-kantoc-(yaponiya).jpg)
Рис. 7(б). Акустический блок установки фирмы Kantoc (Япония)
В установке Karcs II фирмы Kantoc (рис. 7) для обнаружения поверхностных и подповерхностных дефектов используют поверхностные волны. Как указывают создатели установки, контроль с использованием поверхностных волн предпочтительнее вихретокового, поскольку вихревые токи реагируют не только на дефекты, но и на структурные изменения поверхности. Поверхностные волны позволяют обнаружить более мелкие дефекты. Для ввода ультразвука используется контактный вариант. В качестве контактной жидкости используется вода. Однако поверхностные волны очень чувствительны не только к поверхностным дефектам, но и к каплям жидкости на поверхности валка. Для предотвращения попадания жидкости на поверхности прокатного валка применяется специальная система (рис. 7б), которая включает в себя щетки перед ПЭП и пневматическую систему сдува воды. Производителем приведены следующие данные чувствительности установки по выявлению трещин: длина 0,5 – 2 мм, глубина 0,1 – 0,2 мм, раскрытие 0,2 мм. Хотя было заявлено, что УЗК с использованием поверхностных волн позволит добиться большей чувствительности, чем вихретоковый контроль, указанные величины не подтверждают это.
Во всех зарубежных установках контролю подвергаются только бочки валков, шейки не контролируются. Сами установки довольно громоздки и занимают много места. Во всех установках применяется автоматизированная подача блока преобразователей на бочку валка и отвод после завершения контроля.
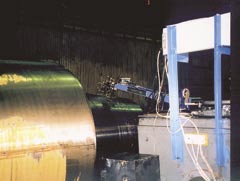
Рис. 8. Установка ВАЛОК-5
С учетом зарубежного опыта и пожеланий металлургических заводов в ФГУП ЦНИИТМАШ были разработаны автоматизированные установки для контроля рабочих и опорных валков ВА ЛОКВТ, ВАЛОК-5 и ВАЛОК-9 (рис. 8). Все установки отличаются портативностью. Конструктивно они выполнены в виде пылевлагозащищенных приборных моноблоков, размещаемых на свободном участке станины (площадки) вальцешлифовального станка. Съемный механизм сканирования, предназначенный для фиксации блока преобразователей на поверхности валка, крепится на свободном месте суппорта станка. Основное отличие данных установок от зарубежных аналогов – это дополнительный контроль шеек валка, необходимость которого была установлена в результате анализа причин выхода из строя рабочих валков [2]. По заказу ОАО «Северсталь» разработана нормативно-техническая документация по НК рабочих валков.
Одноканальная установка ВАЛОК-ВТ предназначена для автоматического контроля рабочих и опорных валков прокатных станов. По своему назначению это рабочий инструмент шлифовщика. Процесс управления установкой настолько прост, что доступен шлифовщику и не требует от него знаний и квалификации специалиста по НК. В установке используется только широкозахватный вихретоковый преобразователь, что позволяет обнаруживать поверхностные и подповерхностные дефекты на глубинах до 3 мм. Результаты контроля выводятся на цветной дисплей в виде двухмерной развертки. Шлифовщик может оценить глубину обнаруженного дефекта и принять решение о вышлифовке дефекта или об отправке валка на более тщательный контроль. Скорость сканирования данной установкой достигает 2 м/с. Рабочий валок может быть проконтролирован за 10 мин, а опорный – за 15 мин. Это время включает в себя и контроль шеек.
Девятиканальная установка ВАЛОК-9 является наиболее функционально насыщенной и не имеет аналогов. Она разработана для полного контроля валков и может быть использована для контроля толстостенных труб, цилиндров и т. п. в диапазоне диаметров 300 – 2000 мм. С небольшими изменениями она может быть приспособлена для цилиндрических изделий другого диаметра. В зависимости от соотношения окружной скорости вращения объекта и скорости линейного движения суппорта, контроль может производиться за один или несколько проходов блока преобразователей вдоль образующей. Конструкция механизма сканирования разработана так, чтобы в нерабочем положении акустическая система не мешала выполнению операций шлифования. В конце кронштейна размещена подвеска блока преобразователей. Оригинальная конструкция блока преобразователей обеспечивает одинаковое давление и защищена патентом [4].
Для повышения вероятности обнаружения разноориентированных дефектов в установке используются восемь ультразвуковых ПЭП с различными углами ввода. Прямой совмещенный и раздельно-совмещенный ПЭП служат для обнаружения объемных и плоскостных дефектов, ориентированных параллельно образующей. Глубина прозвучивания прямым ПЭП равна половине диаметра бочки. Наклонные ПЭП служат для обнаружения объемных и вертикально ориентированных дефектов на глубину до осевой линии бочки. Установка снабжена каналом вихретокового контроля, параметры которого аналогичны модели ВАЛОК-ВТ.
Девятиканальный дефектоскоп, оснащенный системой ВРЧ, имеет большой цветной дисплей, удобный и простой пользовательский интерфейс. В процессе контроля на дисплей выводится эскиз валка с перемещающимся в реальном времени изображением акустического блока. Данные ПЭП и датчиков позиционирования поступают в компьютерную систему. Система позиционирования состоит из датчиков вращения и поперечного перемещения. Она позволяет с высокой точностью (до 2 мм) определять положение блока преобразователей.
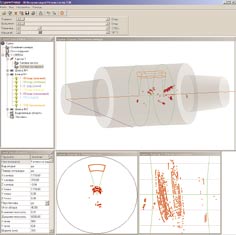
Рис. 9. Программа 3D визуализации установок ВАЛОК
Результаты контроля через беспроводную сеть передаются на компьютер. Программное обеспечение, работающее под управлением операционной системы WINDOWS XP, на основе полученных данных строит объемную модель валка. Программа визуализации позволяет вращать объемную модель валка в трех измерениях (рис. 9). Имеется возможность получения любого сечения в радиальной плоскости. Дефектоскопист может выделить зоны с дефектами и измерить их площадь. Все выделенные сечения и ракурсы опасных дефектов сохраняются в виде закладок и содержатся вместе с файлами данных контроля. Дефектоскопист после изучения результатов контроля на разных уровнях чувствительности подготавливает заключение. Все результаты контроля сохраняются на жестком диске компьютера с возможностью записи данных на другой носитель.
Установка ВАЛОК-5 занимает промежуточное положение в модельном ряде. Ее основная область применения – это контроль чугунных валков, а основные технические характеристики и способ визуализации такие же, как у установки ВАЛОК-9. УЗК ведется на 4 каналах. Один канал используется для вихретокового контроля.
Применение установок НК на металлургических заводах позволит:
- Осуществить первичную паспортизацию валков;
- Своевременно обнаруживать дефекты и проводить мониторинг валка (следить за развитием дефектов) в процессе эксплуатации;
- Уменьшить количество аварийных разрушений валков;
- Увеличить количество перевалок рабочих валков.
Окупаемость автоматизированных установок для контроля прокатных валков в зависимости от модели составит от 6 до 18 месяцев.